What Does 3D Printing Mean for the Future of Part Manufacturers
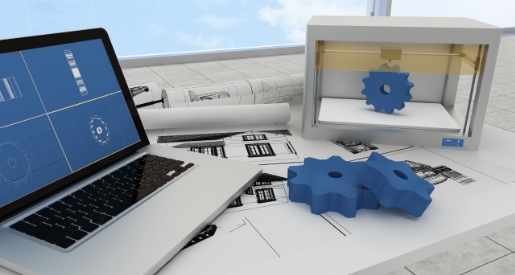
What Does 3D Printing Mean for the Future of Part Manufacturers
What Does 3D Printing Mean for the Future of Part Manufacturers
April 16, 2015
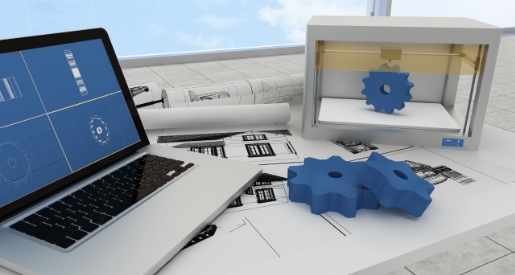
Sometimes, the best way to know the future is to understand the past.
3D printing technology first appeared on the manufacturing scene in the 1980’s. The history however, dates back considerably further. The roots of the idea can be traced back to 1892, when a man named Blanther decided to make a 3D topographical map by cutting the contours of areas on the map in relation to their elevation. By then stacking these contours on top of one another, he was able to create what is undoubtedly the first 3D map.
The idea of creating 3D models from an existing object is historically known as photosculpture, an idea which dates back to 1860. It was in that year when an artist named Francois Willeme surrounded an object with 24 separate cameras and captured the images simultaneously. Using the silhouette of each photo he was then able to carve an exact replica.
Later in 1935, A Japanese man named Morioka combined the topographical and photosculpture concepts to develop a process using structured light to create contour lines of an object which could then be developed into sheets and stacked, generating an accurate 3D model of the object.
These technologies, which became known as Solid Freeform Fabrication, are what we know today as Rapid Prototyping. With the advent of 3D computer software such as Solidworks® and Pro-E® the process of creating dimensional data became much simpler, allowing modern day designers to create highly detailed models using concepts very similar to those in the past.
Current 3D printing technology uses a photo sensitive polymer to produce thin slices of material based on data provided by the 3D program. By then stacking these slices just as Morioka did, exact replicas of the concept drawing are created. This powerful tool allows manufacturers the ability to validate design, develop accurate molds and tooling, and provide customers a prototype product with limited production costs.
The RP process is under constant development, with great strides being made to bring the idea from prototype to limited production status. As the technology matures, new and innovative polymer media is under development that could provide parts that are not only replicas, but useable. In addition, many of the RP applications have now become freeware, allowing even casual hobbyists to set their minds to creating revolutionary applications limited only by imagination.
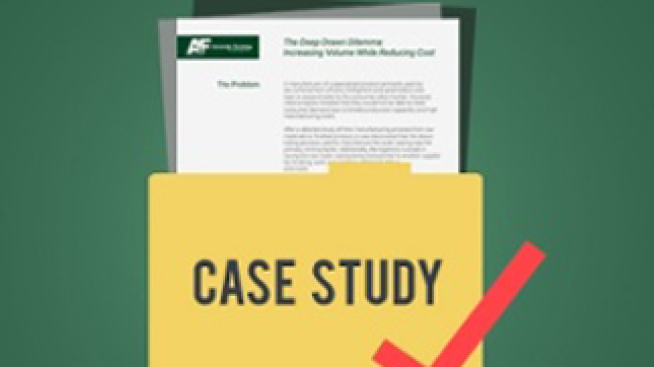