Things to Consider When Having Small Deep Drawn Parts Made
Things to Consider When Having Small Deep Drawn Parts Made
April 21, 2015
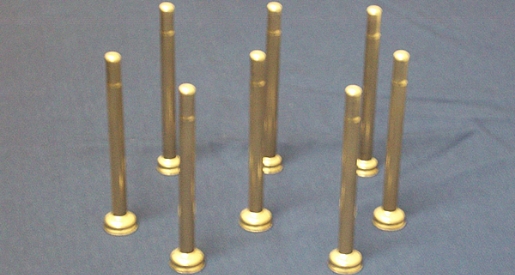
They say that the devil is in the details. Anyone who has managed an engineering or manufacturing project will certainly attest to the validity of that statement. When the decision has been made to change the manufacturing method of a part from one method to another, it’s the fine details that can often be overlooked and add up to major issues down the road.
Developing new small deep drawn parts, or converting the manufacturing method of existing products, requires detailed planning, careful consideration, and a vast amount of knowledge regarding the pros and cons. Every manufacturing method has them; the trick is to balance the design criteria of the product with the best choice.
Producing small deep drawn parts that are smaller in dimension that what may be typical creates a few details that should be carefully considered in order to provide the highest quality part at the best cost available.
Know Your Material
There are two key features of every material that can help determine the success of a deep drawn process. As parts become smaller, these factors become even more important. First is called the “N” value, which is the ability of the material to stretch. Second is the “R” value, or the plastic strain value, that determines the ability of the material to flow. A good supplier will be happy to discuss these details with the customer.
Understand the Design
While this may seem self-evident, understanding the product design as it relates to the deep drawn process can be very important. Consider the wall thickness of the part, the final drawn depth, and the concentricity of the design. These are all critical factors that can decide the quality of the final part.
Rapid Prototype
Rapid prototype machines are a relatively new technology. This process allows the designer and the customer to produce prototype parts using a 3D printer without incurring production costs. With this technology, part concept can be validated before any tooling is created. When developing small deep drawn parts, this process can be very valuable to determine tooling design and feasibility.
A qualified deep drawn supplier will be able to provide much of the information needed to make the best decision. For the customer, knowing what some of the challenges might be provides the knowledge needed to choose the best supplier, and produce the best products.
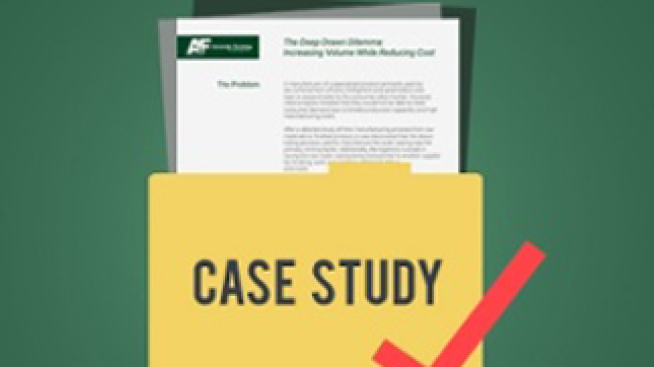