Inside the Design of Writing Instruments 7
Inside the Design of Writing Instruments 7
Inside the Design of Writing Instruments 7
October 10, 2018
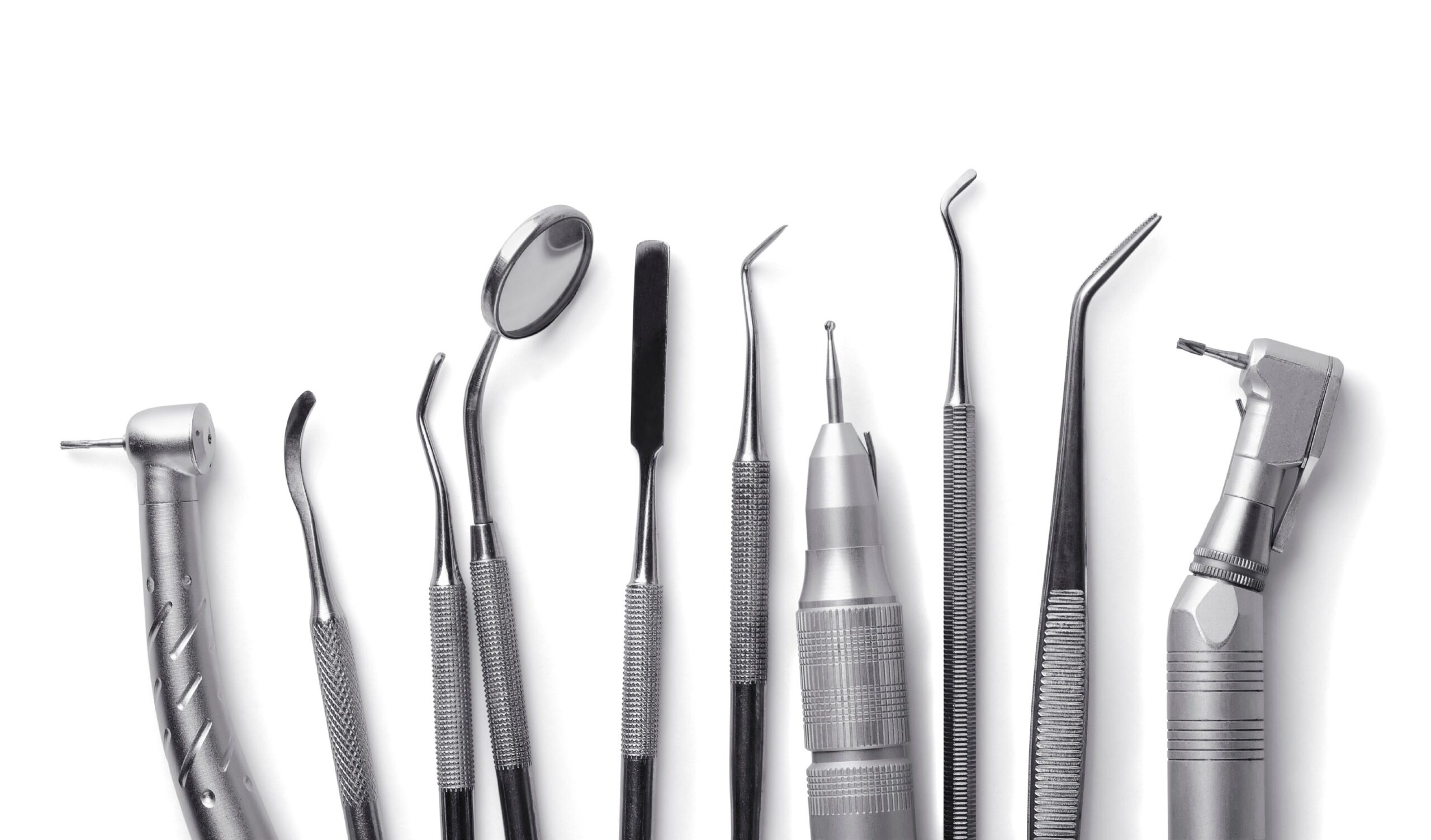
All manufacturers face challenges. Some of the most common being bottlenecks or limitations to their processes which force higher costs than necessary,thus limiting their markets potential. These challenges can be made even more acute when spread over different vendors or situations where one limitation might cause a cascading effect with other vendors, creating even more challenges that can be potentially catastrophic. While identifying these limitations are essential, the question arises how to resolve them effectively thus maximizing the benefits of both the opportunity and resolution. One company found a way to do just that.
A specialized manufacturer was engaging in an expansion from the their current successful niche market to a more consumer oriented market, when analysis discovered a serious limitation that would have adverse effects on not only the expansion but any successful penetration in the consumer arena. Specifically the limitation, in this situation of a manufacturing bottleneck, was a critical part that required excessive production times thereby increasing the manufacturing costs that would inhibit consumer adoption. In addition, having to transport the part from one location to another under the control of a vendor, this created long term delays that would have further deteriorated the potential market expansion. These circumstances forced the company to seek a solution to the limitation and create an opportunity with Accurate Forming that would enhance their expansion instead of just dealing with the issues at hand.
By considering a deep drawing manufacturer for a potential solution, they worked with Accurate Forming to engineer a solution that would not only resolve the bottleneck, but in turn also reduce the inhibiting cost factor while reducing transit times and improve overall quality of both the individual part and the end product. By working with the engineers at Accurate Forming, it was clear that the deep drawing process created a beneficial opportunity for the company. The ultimate result of which was the ability to reduce per unit costs by fifty percent and improve both transit and delivery times. Thus enabling a proper and successful expansion into the consumer market.
What can be derived from this case study or situation is that by seeking to alter a challenge into an opportunity, your company has the potential to improve not only the bottom line but a whole lot more with Accurate Forming’s deep drawn process. By working with our engineers, the end result can prove to be more successful than other manufacturing processes. For a more detailed description and to learn how it was done, download the case study and see the benefits of deep drawing for yourself.
It has long been understood that pressing or stamping is an economical method for manufacturing complex parts. Although there’s a relatively high initial cost to manufacture tooling, deep drawn stamping is usually cheaper and always faster than alternative processes such as machining, fabrication and injection molding.
Deep drawing takes this a step further in that it is possible to produce parts that are longer or deeper than can be achieved through conventional stamping processes.
Deep drawing is a form of metal stamping where the depth of the draw is typically greater than its diameter. In practice, it is possible to produce long, narrow, cylindrical parts with a length that is significantly greater than the outside diameter of the part.
Conventional stamping processes are unable to achieve such deep draws because the material’s cannot stretch sufficiently resulting in uneven wall thickness, thinning and tears. In deep drawing, this challenge is overcome by careful tool design that forces material to flow into the die during the initial stages of the deep drawing process. This ensures that sufficient material is available to achieve the final shape while maintaining the desired wall thickness.
Deep drawing is performed in several stages. During the first stage, the blank will be forced into a cup shape with a larger diameter than the final part diameter. During successive stages, the part diameter is gradually reduced and its depth increased. Tooling is usually ganged together with some form of part transfer so that all operations take place on one press.
Using these techniques it is possible to use deep drawn methodology to manufacture a part that’s more than ten times longer than its outside diameter.
The design of deep drawn tooling is crucial. Special care needs to be taken to ensure that excessive stretching does not take place, and for this reason the initial die and punch radii need to be carefully calculated. If the die radius is too small, material will not flow properly, and if it’s too great, wrinkling will occur. All tooling should be highly polished to aid material flow and high-strength tool steel used for the radius at the die entrance.
The clearance between the cup and tool is also critical to ensure the correct final ratios between stretch, flow and work hardening. The press speed is important because if it’s too high, corner cracking will occur, but if too low, material flow will be affected.
There are two major advantages of deep drawing. Firstly, production volumes are high and are only limited by the speed of the press, and press capacity usually exceeds 2,000 parts per hour. Secondly, the finish achieved is such that no further processing is required, and secondary operations such as beading, notching, chamfering and piercing can be performed within the deep draw tooling.
Due to these two factors, the cost per part is low even after tooling costs are taken into account.
Parts that are symmetrical with a round or oval shape and a length to diameter ratio that’s less than 10 are usually good candidates for deep drawing. Additionally, deep drawn stamping can be performed with an almost unlimited range of materials including steels, alloys, aluminum, brass and copper. Thanks to the natural work hardening that takes place, parts are strong, light and can be manufactured to exacting tolerances. Most importantly, parts that are suitable for deep drawing are often ones that are difficult and expensive to manufacture by alternative processes.