Hidden Costs of Using a Foreign Manufacturer
Hidden Costs of Using a Foreign Manufacturer
Hidden Costs of Using a Foreign Manufacturer
September 1, 2015
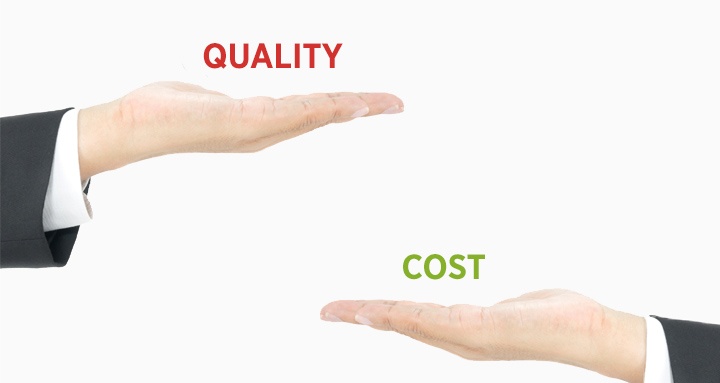
While outsourcing to a foreign manufacturer might seem like a cost effective solution, going with a foreign supplier is not without peril. Not all foreign suppliers adhere to the necessary standards and practices involved with manufacturing. Additionally, issues with quality control, material quality and difficulty of communication can create problems and issues that can affect the overall production and delivery of the product. When looking for a foreign manufacturer for your product, remember a foreign manufacturer is under no obligation to put you, the customer, first.
As experience has shown, in the 2007 and subsequent Mattel toy recalls, quality of materials is not always in place with foreign manufacturing. In many cases, foreign manufacturers rely on a volume business model that dictates using lesser quality materials for a higher return. This can contrast directly with other companies who use the quality assurance/customer first business model. While some foreign manufacturers will express a willingness to partner to develop a quality solution, many are only concerned about their needs and not that of their customer.
Everything previously mentioned about material quality can also be applied to quality control methodologies and practices in some foreign manufacturers. Minor defects in manufacturing are ignored as it is not recognized as a potential failure point during long term use. Other issues related to quality control is improper training, lack of effective quality communication and a lack of understanding towards customer expectations and needs. All of which has a negative effect on quality control in many foreign manufacturers. Often this is due to a cultural difference and not a willingness on the manufacturer to produce defective parts.
Design specifications produced in one country and required in another for actual production or manufacturer can be inhibited by the communication barrier. While attempts are commonly made to address any communication difficulty, on critical components subtle differences can occur in the different meanings of words. This can lead to manufacturing problems, delays and even defective parts that can compromise the overall project.
While working with a foreign manufacturer might be cost effective in the short term, long term it is more efficient and effective to go with a domestic supplier or manufacturer when possible. The per unit cost might be higher but what is gained in quality, lack of cultural differences and communication differences, low delivery costs, better inventory programs (compound over bulk) is better for your company.
When looking for a supplier for deep drawn components for your business, getting the right supplier or manufacturer is vital to your success. There are many suppliers but often there are more suppliers or manufacturers that will not meet your exact need than will. It goes beyond the single issue of part cost. Quality of materials, workmanship, quality control and total price with intangible costs all play a role in finding the right supplier.
Medical equipment is manufactured to the highest standards to ensure components exhibit the right combination of characteristics such as adequate strength, proper functionality, easy sterilization and ease of manufacture. Irrespective of where or how medical components are used, healthcare staff must have confidence that they will perform the required function flawlessly with no risk of patient infection.
The size of medical components is always a critical factor because medical tools need to be easy to handle and in many applications, such as in dentistry, the components need to be small and strong. These requirements can be met by using deep drawing production processes, which are able to produce tubular components that are compact, yet light and strong. Deep drawing can produce parts with height-to-width ratios of 8:1 for stainless steel and greater than that for more malleable materials.
A major benefit of deep drawing is that parts produced are seamless without joints or imperfections. There are no awkward nooks, crevices and sharp angles to trap bacteria. The natural work hardening that occurs during the process means that parts produced are strong. Material thickness of parts can be tightly controlled and the process allows the manufacture of flawless parts that are extremely thin.
Unlike many other manufacturing processes, deep drawn parts have an excellent surface finish that in many instances needs no further treatment. These finishes are highly amenable to further polishing to provide a mirror-like finish. Alternative finishes, such as nickel and chrome plating, may be applied with the further advantage of being able to obtain a guaranteed 100 percent internal and external coverage.
All of this is achieved at a lower unit cost than is possible with many other manufacturing processes. Unit production costs are low especially if automated part feeding equipment is used. Naturally, the relatively high initial cost of deep drawing dies and other tooling needs to be recovered, but provided the production volumes are reasonably high, the amortized production costs for deep drawn medical parts are low.
The use of deep drawing production processes for medical components offers many advantages. Unit production costs are minimal, and parts produced are strong and have a high quality finish without any surface defects that could cause infection. Tight manufacturing tolerances can be easily achieved, and a wide range of finishes are available that include highly polished nickel and chrome plating and powder coating.
The manufacture of components for medical equipment is governed by the FDA. Medical equipment manufacturers must be registered and the devices they manufacture specifically listed.
The list post is one of the most popular and readable blog formats on the web. It is composed of — you guessed it — a list, and includes short explanatory paragraphs about each item.
Use your introduction as a way to tell the reader how this collection of ideas will help them. Keep it light by including a personal story. If you have any data that you can include relating to your list, include that in your introduction, too.
Here are some examples of how we use list blog posts here at HubSpot:
Now deliver what you promised in the first section. This is the longest part of the post, so make it easy to read. Use short paragraphs, bullet lists, and bold headings to set different sections apart.
Some common section headers include:
You can use bulleted lists, numbered list, or multiple headings. Include as many steps, numbers, or bullets that will allow you to discuss your topic thoroughly.
Here are some pointers to make the best possible body of your blog:
Now it’s time to say goodbye and wrap up your post. Remind your readers of your key takeaway, reiterate what your readers need to do to get the desired result, and ask a question about how they see the topic to encourage comments and conversation. Don’t forget to include a Call-to-Action!
Congratulations! What a lovely list post you’ve created!
One vital and critical area of the medical arena, especially in facilities, is infection control. Simply put, infection control is the reduction or elimination of infectious elements and the procedures and materials necessary to prevent secondary infections of both personnel and patients
In reference to the materials aspect, this includes implantable and external medical devices and components. Therefore all aspects of any device or component must be designed and engineered with infection control in mind, and this is where deep drawn medical components are superior in form and function.
Deep drawn medical components and medical devices offer the ability to maintain consistent control of device or component during the manufacturing process and thus are able to provide for a uniform surface that can then be finished in such a manner as to reduce adherence by infectious agents. This, along with other infectious controls at the medical facility, reduces the likelihood of a secondary infection. However deep drawn components offer more than infection reduction.
The deep drawing manufacturing process aligns several factors, quality of the inherent material, sturdiness of design, and reliability of the specific part along with the previously mentioned infection reduction role. This complete system of processes allows for medical devices that are of the highest quality and dependability, as would be expected in a component vital for life. When one realizes that cases, shells, housings, cans, and other components are necessary for continued living and well being due to being part of medical devices and applications, it is clear why deep drawn components are superior to other components created by other methods.
Naturally, in order to reap the benefits of deep drawn medical components, one must partner with a manufacturer that is fully experienced in the deep drawing method and has the knowledge and skillset to deliver the highest quality components. In a real sense, deep drawn medical components saves lives but only if they are constructed and manufacturer with a total commitment to excellence.
At one time there was a belief that society would become paperless, but despite the widespread uses of tablets, laptops and smartphones, paper is still extremely popular. It seems the world is not yet ready to give up on handwriting methods and, in particular, the use of marker pens.