How Deep Drawn Manufacturing Can Expand Your Production Capacity
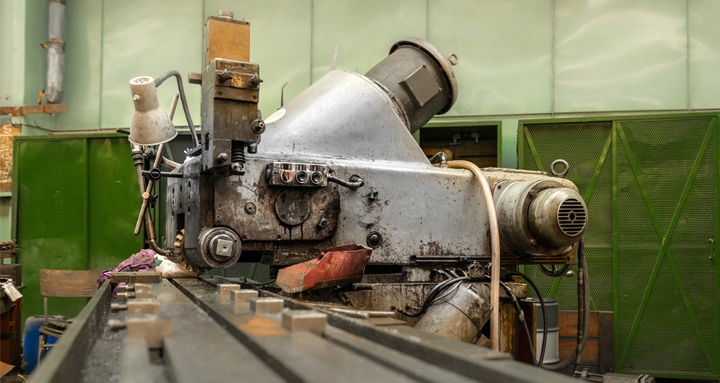
How Deep Drawn Manufacturing Can Expand Your Production Capacity
How Deep Drawn Manufacturing Can Expand Your Production Capacity
January 19, 2016
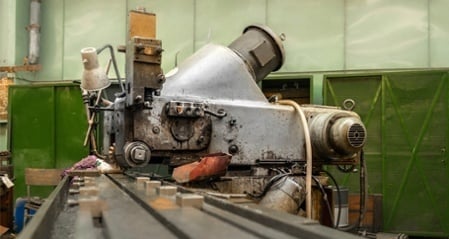
Deep drawn manufacturing of small cylindrical components offers numerous advantages over other manufacturing methods and usually results in lower costs, increased productivity and higher quality finishes.
Deep Drawn Manufacturing
The key to successful deep drawn manufacturing is careful design of the tooling. For relatively shallow lengths, it’s usually possible to stamp the part progressively, but the deep draw process requires several drawing stages on a transfer press. The manufacture of deep drawn tooling is complex and requires a specialist knowledge of both the process and material properties.
Alternative Processes
The most common alternative methods of manufacturing small cylindrical components with a high length to diameter ratio are to machine the parts out of solid stock or from special tubing.
Although machining is capable of providing an excellent finish, it’s extremely difficult to achieve the low wall thicknesses that are often required, and the machining process is slower, leading to high machining costs. Repeatability, dimensional stability and quality are easily affected by tool wear, It’s not unusual for the overall reject rate to be higher in the machining process.
It’s for this reason that some manufacturers use special tubing to manufacture these parts. Generally, this requires the supply of specially drawn tubing with appropriate internal and external dimensions and such tubing is expensive. Additionally, it’s not easy to produce rounded or closed end profiles from tubing. The manufacture of cylindrical parts from tubing is slow, and due to high raw material costs, expensive.
Benefits of Deep Drawn Manufacturing
It is well known that the fastest way to produce a part is to stamp it on a press, particularly when automated raw material feed and transfer systems are used. The only factors limiting output are the setup time and the stroke rate of the presses. Although tooling costs are more expensive than machining tooling, the high throughput achievable along with low raw material costs and less scrap generated per part and faster cycle times means that the cost of each part is much lower than alternative processes.
Other benefits include high repeatability, excellent dimensional stability, an ability to achieve low wall thickness and minimal fall-off rates. The final product quality is high, and often it’s possible to dispense with further finishing processes apart from polishing or applying suitable coatings.
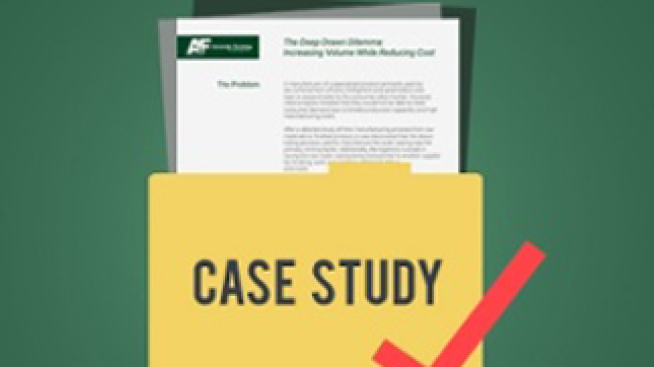