How Deep Drawn Can Reduce Your Manufacturing Costs
How Deep Drawn Can Reduce Your Manufacturing Costs
January 26, 2016
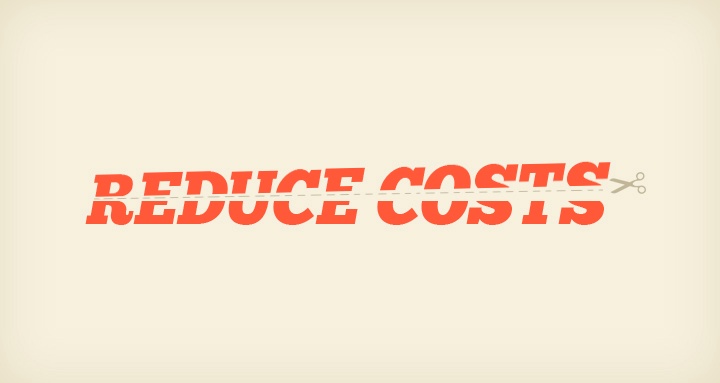
Although the initial investment in deep drawn tooling is more costly, the manufacturing costs of deep drawn components are significantly lower than other processes, especially when high annual component volumes help amortize the tooling costs.
The point at which deep drawn manufacturing becomes competitive depends on production volumes, complexity of the part and comparative costs of manufacturing processes. Here are several ways that deep drawn manufacturing reduces manufacturing costs.
Shorter Lead Time
Once tooled Deep drawn manufacture is fast and capable of producing high volumes compared to other manufacturing processes. Most deep draw presses are able to exceed production volumes of over 5 parts per minute, depending on material, gage and transfer systems used. Thanks to this high production volume capability, it’s possible to ensure a short lead time from order to delivery of components. This reduces inventory costs and allows manufacturers to adopt just-in-time manufacturing practices. Notably, the lead time for component delivery is significantly shorter than for alternative manufacturing processes.
Lower Component Costs
Raw material costs are lower than for other manufacturing processes. This is because parts are blanked from coiled strip. No special preparation is required apart from ensuring cleanliness and that the raw material complies with specification. Alternative processes use solid billets or specially drawn tubing, which are more expensive to procure. The conversion cost of deep drawn components is low so it’s possible to significantly reduce costs.
Labor Costs
The cost of labor associated with the production of deep drawn parts is very low. Presses are normally fitted with automated feed systems. Depending upon the part size and availability of suitable material, blanks may be cut directly off coil in the press or loaded individually. Automated transfer systems move parts through each stage and completed parts are ejected automatically. Consequently, a deep draw press requires minimal supervision, and depending upon the level of automation, usually requires only one operator.
Low Overhead Costs
Equipment is durable and long lasting. Maintenance requirements for well-designed tooling are moderate and overall costs are not excessive when production capacities are taken into account.
These overhead costs are normally allocated on a pro rata basis to each part manufactured. Provided press utilization is high and production volumes are reasonable, the overhead cost carried by each part manufactured is minimal and compares favorably with the overhead costs of dedicated alternative manufacturing facilities.
Low Wastage
The fall-off rate of parts manufactured in a deep draw press fitted with well-designed tooling is low. Parts have consistent dimensions and, with careful tooling design, tight tolerances are possible. Overall reject rates are low.
The other major source of waste, that is, scrap material, is limited particularly if blanks are cut in such a way as to minimize coil wastage. Additionally, off-cuts and webs can be recovered and sold to raw material suppliers for reprocessing.
Explore the Advantages and Reduce Manufacturing Costs
The deep drawn manufacture of thin walled, cylindrical components is faster, easier and simpler than is possible with alternative manufacturing methods.The quality of the finished component is high, and it’s possible to achieve tighter tolerances. The aesthetic appearance of parts straight off the press is good, and further finishing such as polishing, plating or coating is viable.
Unit production costs are low, and overhead costs associated with deep drawn tooling are recoverable over the life of the component. In any event, the cost of specialized deep draw tooling is in many cases lower than the costs of alternative equipment and tooling to manufacture complex, high tolerance, cylindrical components.
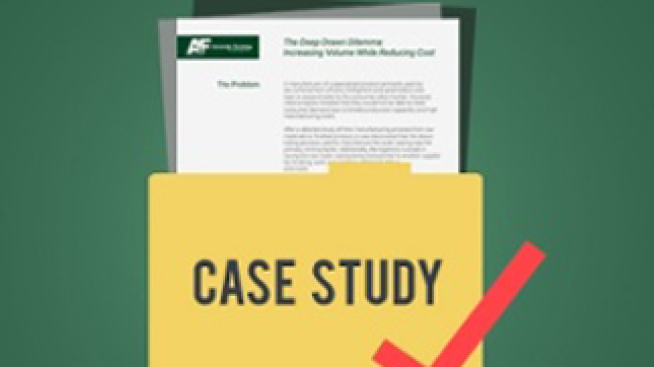