How to Identify If Your Current Manufacturing Process Takes Too Much Time
How to Identify If Your Current Manufacturing Process Takes Too Much Time
December 22, 2015
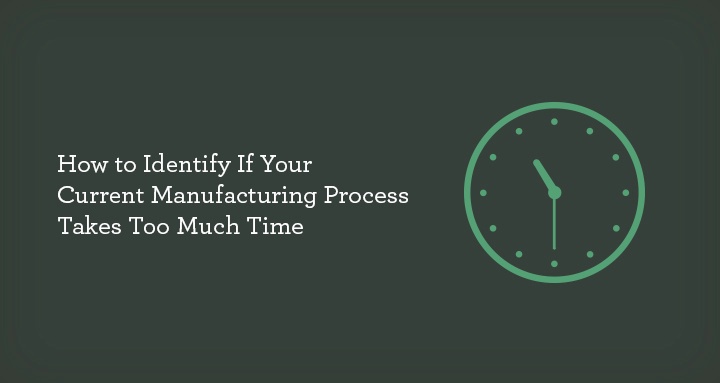
Many devices used by industry, law enforcement and other agencies have a cylindrical shape. Typical examples include pencil torches, writing and marking instruments and medical devices. The outer casing may be open at both ends, at one end only or be domed. For cosmetic or functional reasons, the outer casing is often polished, anodized, powder coated or plated.
The manufacture of these devices is often tricky due to the need to maintain tight tolerances and ensure functionality. Frequently, what appears to be a relatively simple operation becomes a limiting factor on production lines. Here are some tips to identify if your manufacturing process is taking too long.
Production Capacity Cannot Meet Demand
One fairly obvious symptom is when supply and demand are not in balance, and manufacturing cannot keep up with regular demand. Although it’s easy to identify this when the plant capacity is clearly below demand, in other situations it may be a particular production issue that is limiting capacity in a line, which according to its nameplate capacity, should be able to meet demand. This is often characterized by actual production being consistently lower than forecast and when it’s not always easy to identify the underlying reasons.
Inability to Respond To Sudden Orders
Related to the above point is a situation when the line is constrained and cannot flex production capacity to meet additional orders, particularly those from customers wanting fast delivery. These missed opportunities often mean that revenue is lower than expected and profitability is reduced.
Where’s the Bottleneck?
In most cases, an inability to meet demand is due to a bottleneck. Correct identification of the reason why is sometimes difficult because, for a multitude or reasons, the underlying cause is masked.
One way to check is to monitor the line’s output at various points, measuring utilization, downtime and output to help identify the real cause. It’s likely to be in an area where the manufacturing process is too slow. This may be due to quality issues or a production process with too many operations. Often, these relate to difficult processes where it’s difficult to achieve the tolerance and required finish.
Quality Control Issues
Identify operations where the manufacturing process is incapable of producing the requisite quality continuously. This may happen when the process requires manual dexterity and skill or the tooling is not up to the job. It may also be that the required tolerances are difficult to achieve with the current manufacturing process, resulting in excessive scrap and poor production.
Aesthetic Appearance
Another possibility is difficulty in achieving the required surface finish, leading to high rejects and customer complaints. This often relates to the manufacture of the outer casing and difficulty in obtaining the required profile. If this is the case, not only is it a cause for concern, but a poor finish affects the marketability of the product and its application in critical applications.
Deep Drawn Manufacturing May Be the Answer
An inability to achieve the required quality during the manufacture of cylindrical parts is often responsible for slow production, particularly if tolerances are tight. Parts may be machined from a solid piece of material or manufactured from specially drawn tubing. In both instances, difficulties achieving the required profile and wall thickness slow the line, particularly as thin walled parts are easily damaged.
A solution is deep drawn manufacture of cylindrical parts. This manufacturing process can produce complex cylindrical shapes with wall thicknesses down to .007 inches. Finish is good as is the ability to maintain tight tolerances. Overall costs are low, and the high speed presses are used remove production constraints.
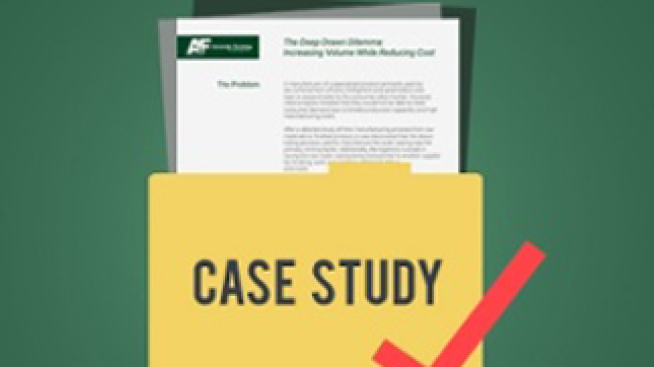