3 Most Commonly Asked Questions About the Deep Drawn Forming Process
3 Most Commonly Asked Questions About the Deep Drawn Forming Process
May 14, 2015
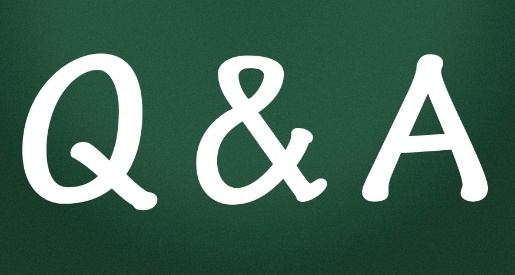
The deep draw forming process is rapidly gaining popularity as one of the most cost effective and sought after methods of manufacturing, and with good reason. The process is capable of creating parts from a vast number of different materials quickly, efficiently, and at low cost, generating plenty of interest from markets all over the world.
Like any technology, there are still plenty of questions about the process that need answers. Here then, are the top three most commonly asked questions regarding the deep draw forming process.
Q: My part is pretty complex. Can the deep drawn process handle complex geometries?
A: You bet. The deep draw forming process uses multi-stage dies that can make a series of different shapes to the part one after the other. By starting with a basic shape and adding contours, curves, slots and many other features, the process can produce parts with some very intricate designs. Add to that available value added operations such as powder coating, name stamping, and finishing, and the deep draw process becomes an almost one-stop solution.
Q: Dies are very expensive. Isn’t it cheaper to use machining centers?
A: While there is cost associated with the initial die, once the process is underway the high production rates more than compensate for initial cost. The deep draw process is low maintenance and requires very little labor, making it one of the most cost effective methods around on a part per part basis. Using in-house precision machine shops, most deep draw suppliers have the tools and experience to keep your die healthy and running smooth for a long, long time.
Q: Is the deep drawn forming process limited by material type?
A: The deep draw process can handle materials ranging from stainless steel to custom alloys. Even the toughest metals can be deep drawn using the right die and press set-ups and plenty of experience. Aluminum, brass, copper, even tin plate can all be deep drawn with ease, resulting in quality parts for hundreds of applications.
With low maintenance costs, minimal labor, and high quality standards all at the lowest per part prices of almost any manufacturing method, it becomes obvious why the deep draw forming process is gaining such a strong following. As technology advances so does the industry, creating a future limited only by imagination.
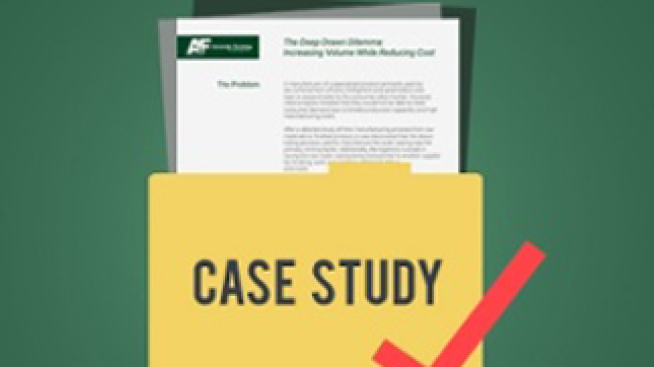